Contributed by: KNM Management Advisory
Explore the ins and outs of job order costing in this comprehensive guide. Why is it important for businesses? How can it help organizations effectively manage costs? And what can we learn to make informed financial decisions?
Whether you are a business owner, manager, or aspiring professional in the field of finance, this article will provide you with valuable insights into job order costing and its practical implementation.
Aspects covered:
- What is Job Order Costing?
- Importance of Job Order Costing
- Key Elements of Job Order Costing
- Direct Materials
- Direct Labor
- Overhead Costs
- Steps in Job Order Costing
- Identifying Cost Objects
- Accumulating Direct Materials Costs
- Tracking Direct Labor Costs
- Allocating Overhead Costs
- Computing Total Job Costs
- Job Order Costing vs Process Costing
- Benefits and Limitations of Job Order Costing
- Real-World Examples of Job Order Costing
- Implementing Job Order Costing in Your Organization
- Conclusion
Job Order Costing?
Job order costing is a costing method used by businesses to determine the costs associated with producing unique products or providing specific services.
It involves tracking and accumulating costs for each individual job, project, or order. Job order costing is particularly suitable for industries such as construction, custom manufacturing, printing, and professional services, where products or services are tailored to meet the specific requirements of customers.
Importance of Job Order Costing
Job order costing provides several benefits to businesses. Firstly, it enables accurate cost estimation for each job, allowing organizations to set competitive prices, maximize profitability, and make informed business decisions.
Additionally, job order costing facilitates effective cost control by identifying cost variances, analyzing their causes, and implementing corrective actions. It also helps businesses assess the profitability of different jobs, clients, or projects, aiding in strategic decision-making and resource allocation.
Key Elements of Job Order Costing
Job order costing comprises three primary cost elements: direct materials, direct labour, and overhead costs.
Direct materials include the raw materials specifically used for a particular job. Direct labour refers to the wages or salaries of employees directly involved in the production or provision of the job.
Overhead costs encompass indirect expenses, such as rent, utilities, equipment depreciation, and administrative costs, which are allocated to each job based on a predetermined cost allocation method.
Steps in Job Order Costing
To implement job order costing effectively, businesses follow a series of steps:
Identifying Cost Objects: Cost objects are the units or items for which costs are accumulated. They can be products, services, projects, or contracts.
Accumulating Direct Materials Costs: Track and record the cost of direct materials used for each job, including the cost of purchasing, transporting, and storing materials.
Tracking Direct Labor Costs: Monitor and record the labour hours and associated costs incurred by employees working directly on each job.
Allocating Overhead Costs: Determine a suitable method to allocate overhead costs, such as using predetermined rates based on direct labor hours, machine hours, or material costs.
Computing Total Job Costs: Summarize and compute the total job cost by adding the direct materials, direct labor, and allocated overhead costs.
Job Order Costing vs Process Costing
It is essential to differentiate job order costing from process costing, as they are used in different production environments.
Job order costing is applied to unique, customized products or services, while process costing is used for mass-produced, homogeneous goods or continuous services. Understanding the differences between these costing methods allows businesses to choose the most appropriate approach based on their operational characteristics.
Benefits and Limitations of Job Order Costing
Job order costing offers several advantages, including accurate cost tracking, enhanced cost control, and improved decision-making.
However, it also has limitations, such as complexity in tracking costs for multiple jobs simultaneously and potential inaccuracies in estimating overhead costs. By weighing the benefits and limitations, businesses can determine whether job order costing aligns with their specific needs.
Real-World Examples of Job Order Costing
Illustrating the practical application of job order costing, this section presents real-world examples from various industries, such as construction, advertising agencies, and speciality manufacturing. These examples demonstrate how organizations effectively implement job order costing and utilize the resulting cost information to optimize profitability and make informed financial decisions.
Let’s walk through a real example to get a better feel for how this all works.
Imagine a small T-shirt printing company getting a custom order for a limited run of 1,000 T-shirts. How will it calculate the costs of this job?
First, it will add up the costs of the raw materials. The custom order is for 100% cotton T-shirts, so that is the only material involved. The company determines it costs Rs. 0.68 per T-shirt, so it will cost Rs.680 for 1,000 T-shirts (Rs.0.68 * 1,000).
Next, it will need to calculate the labour costs. It needs to employ one worker to operate the machinery for 6 hours to make the T-shirts. This worker is paid Rs.15/hour, so that comes to Rs.90.
After that, the company will need to calculate its overhead rate and allocate the overhead. If it paid Rs.5,000 in overhead last month between rent, utilities, machinery, etc., it could divide this by an activity driver, like the total number of direct labour hours over the same period, to get an overhead rate.
So, if the company had 160 total direct labour hours, the overhead rate would be Rs.31.25 per labour hour (Rs.5,000/160 = Rs.31.25). Then, it will allocate the labour to this job by multiplying the rate by the hours: Rs.31.25 x 6 = Rs.187.50.
Now, simply add up all these expenses to get a total job cost of Rs.957.50 (Rs.680 + Rs.90 + Rs.187.50).
Implementing Job Order Costing in Your Organization
This section provides practical guidelines for implementing job order costing in your organization. It covers aspects like designing a job cost system, setting up cost accounts, establishing cost allocation methods, and leveraging software tools to streamline the process. By following these steps, businesses can successfully implement job order costing and reap its benefits.
Conclusion
Job order costing is a vital tool for businesses seeking to effectively manage costs, accurately estimate job profitability, and make informed financial decisions. By understanding the key elements, steps, benefits, and limitations of job order costing, organizations can implement this costing method successfully.
Whether you are a small business owner or a financial professional, incorporating job order costing practices can provide you with valuable insights into your operations and help you achieve cost efficiency and profitability.
Disclaimer: The information provided in this blog is for educational purposes only and should not be considered professional advice.
Contributed by:
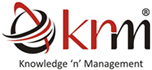
KNM Management Advisory Pvt. Ltd.
Tokyo, Dhaka, Delhi, Gurugram, Chennai, Ahmedabad,
Bangakore, Mumbai & Chandigarh
www.rvkassociates.com
INDIA HEAD OFFICE
Unit No. 508, 5th Floor, Vipul Business Park,
Sector-48, Gurugram-122001, (Delhi-NCR),
Haryana, India
Email: services@knmindia.com
Phone: (+91) 124 429 5170 or (+91) 991 009 5170
JAPAN OFFICE
Mr. Keisuke Takahashi
Ebisu NR Building, 6F
1-21-3 Ebisu, Shibuya-ku
Tokyo 150-0011
Email: japandesk@knmindia.com
Phone: +81-3-6869-0850 or +81-3-6821-9455